What is the Continuous Carbonization Process?
In the field of industrial production, the continuous carbonization process is an important method for transforming materials. It is a thermochemical process that involves the targeted treatment of materials through a series of controlled heating steps. The main goal of the process is to achieve high carbonization yields and consistent quality while minimizing energy consumption.
With the continuous development and updating of technological equipment, in addition to its application in charcoal production, continuous carbonization furnaces can also be used to carbonize and remove paint from cans and recycle aluminum capacitors, waste wires and other metals.
In the continuous carbonization process, the material is fed into the carbonization reactor, which usually takes the form of a rotary kiln. The combustion system heats the kiln to temperatures of 400-600°C, producing hot gases that pass through the biomass material. When the material is heated, volatile compounds such as water, hydrogen and carbon dioxide are released, and the remaining char is carbonized. The combustion of volatile compounds produces thermal energy, which is used to maintain the temperature within the kiln.
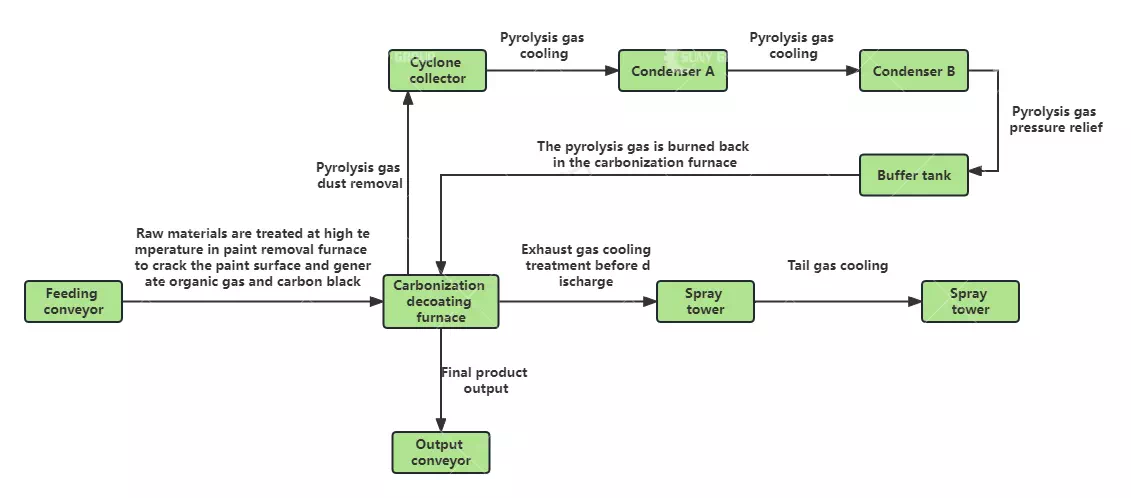
One of the essential features of the continuous carbonization process is the efficient recovery and utilization of the volatile compounds released during the process. These volatile compounds can be burned in the secondary combustion chamber to produce steam or other forms of energy. In some cases, volatile compounds can be condensed and collected as valuable by-products.
After the carbonization process is completed, the material is cooled and discharged from the kiln. The cooling process is crucial because it helps prevent the charcoal from releasing volatile compounds that could ignite and cause an explosion. Cooling can be achieved by a variety of methods, such as water quenching, natural air cooling or the use of cooling jackets.
The continuous carbonization process offers several advantages over traditional intermittent carbonization methods. On the one hand, it can be more efficient, have stable quality, and have minimal impact on the environment. The process also generates energy using the volatile compounds released during carbonization, thereby reducing the overall energy consumption of the production facility.
SUNY GROUP has rich experience and technical equipment in continuous carbonization furnaces, and has applied them in many fields to help customers solve carbonization recovery solutions for different materials. Although the principles are the same, because the materials are different, there are differences in the carbonization process. There will also be changes in . If you are interested in continuous carbonization furnaces, or want to learn about related recycling technologies and equipment, you can contact us at any time for consultation.