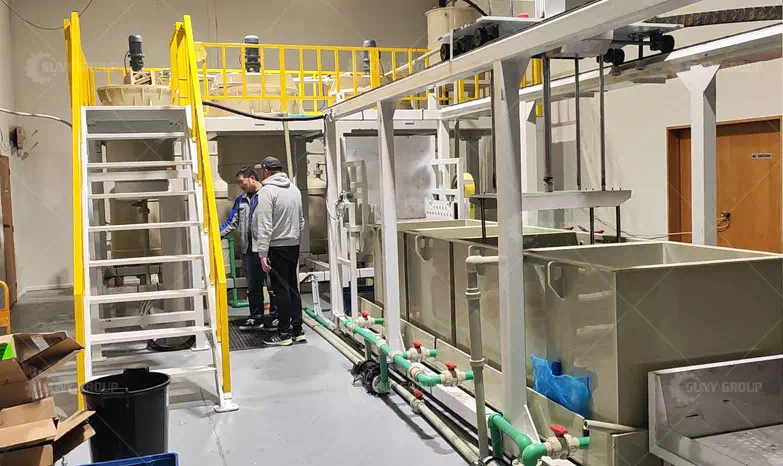
Author: zzsuny
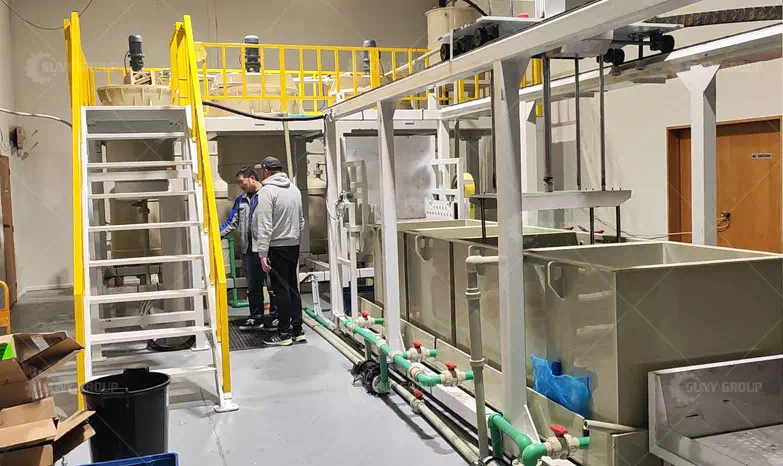
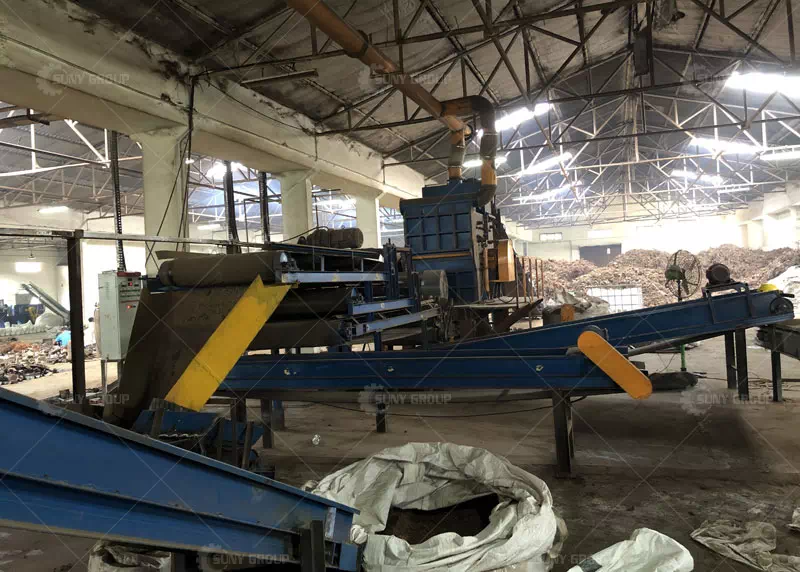
Electric hammer shredders combined with magnetic separation technology play a key role in the recycling of small stators and rotors. Let’s take an in-depth look at the process of recycling used small stators and rotors, from debris processing to material sorting, these steps show how this technology can be effectively utilized.
Hammer Crusher with Magnetic Separation for Recycling Small Stator and Rotors
Recycling Process for Used Small Stators and Rotors
A. Fragmentation
An electric hammer crusher is one of the key pieces of equipment in the recycling process of used motor parts. By rotating the hammerhead at high speed, the Electric Hammer Crusher can effectively crush and process motor parts such as small stators and rotors. This step not only helps to reduce the size of the waste but also provides better conditions for the subsequent magnetic separation process.
B. Magnetic separation process
Magnetic separation technology is an important part implemented in the waste motor parts after treatment in the electric hammer crusher. By utilizing the properties of magnetic materials, the magnetic separation equipment can effectively separate iron-containing materials, such as iron cores, from non-magnetic materials. This process not only improves the recycling efficiency but also effectively reduces the metal content in the waste material and creates better conditions for resource reuse.
C. Material Classification
After the magnetic separation process is completed, the recovered materials need to be classified for further processing and reuse. Depending on the nature and use of the material, the recycled motor parts such as small stators and rotors can be categorized into different types such as metals, plastics, etc. This kind of classification helps to increase the reuse rate of resources, reduce the dependence on natural resources and is also conducive to environmental protection.
The importance of electric hammer crushers combined with magnetic separation technology in recycling small stators and rotors cannot be overstated. This technology not only improves the recycling efficiency of used motor parts and reduces resource wastage, but also helps to minimize the impact on the environment. Through the processes of fragmentation, magnetic separation, and material sorting, used small stators and rotors are effectively recycled and reused, contributing to sustainable development.
Meet Suny Group at the CMRA Show!
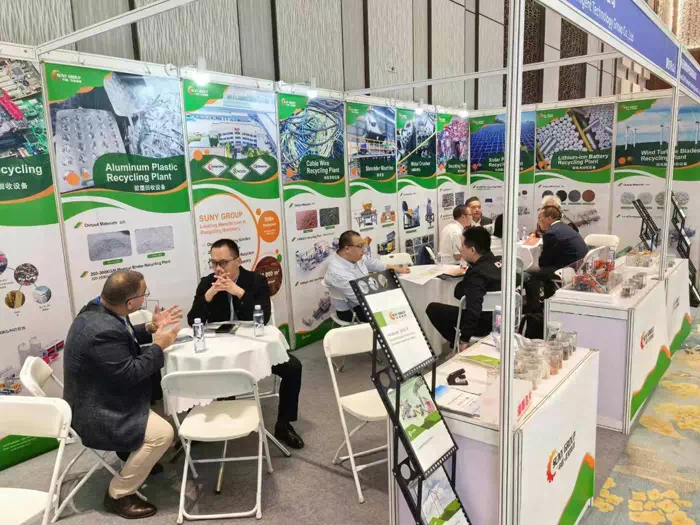
Suny Group Meet You at CMRA Fair, one of the top fair for metal scrap trading and recycling machines.
Date: November 7-9th, 2024
Location: Suzhou, China
Booth No.: C60-C62
Industrial Small Copper Wire Granulator
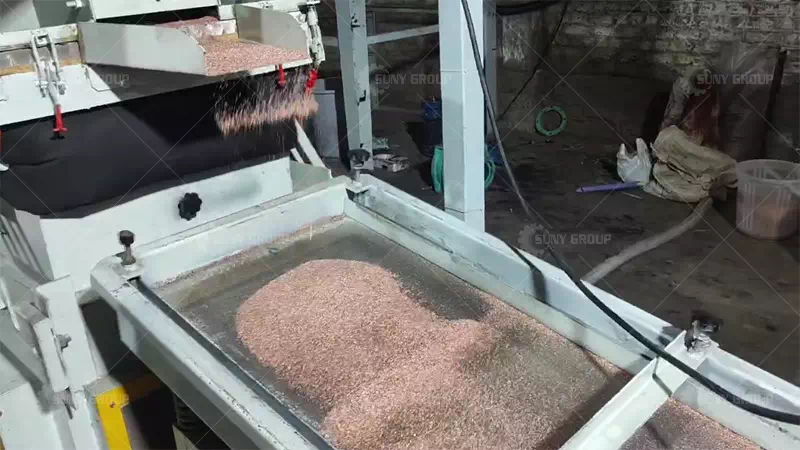
In the industrial sector, small copper wire granulation recycling machine plays an important role in providing efficient solutions for recycling and reusing waste copper wire. Let’s take a closer look at the definition of this equipment, its features and its importance in resource recovery and environmental protection.
The Industrial Small Copper Wire Granulator Recycling Machine is a specially designed equipment for processing waste copper wire. Its main function is to process the waste copper wire and separate the pure copper and plastic for further recycling and reuse.
Features
A. Equipment Specifications and Operating Principle
This type of equipment usually has a compact design and is suitable for use in industrial production sites. The working principle is to convert waste copper wire into reusable copper and plastic granules through a series of crushing, separation and screening processes.
B. Energy efficient features
The industrial small copper wire granulation recycling machine has the characteristics of high efficiency and energy saving, which can maximize the utilization of resources in the recycling process, reduce energy consumption and lower production costs.
C. Scope of application and industry application
This kind of equipment is widely used in the fields of metal recycling, cable manufacturing and environmental protection industry, which provides the related industries with efficient solutions for the treatment of waste copper wires.
Pakistan Copper Wire Granulator Customer Site
Workflow
A. Preliminary treatment stage
In the preliminary treatment stage, the waste copper wire is first collected and processed to prepare for the subsequent pulverization and separation process.
B. Crushing and separation stage
Subsequently, the scrap copper wire passes through the pulverization and separation stage where the copper wire is pulverized into granular form and effectively separated from the plastic.
C. Sorting and Recycling of Pure Copper and Plastic
Finally, the equipment separates the pure copper and plastic through the sorting process, realizing the recycling and reuse of resources.
Advantages
A. Resource recovery and environmental value
The advantage of industrial small copper wire granulation recycling machine is that it can improve the efficiency of resource recycling, reduce the pollution of waste to the environment and realize the sustainable use of resources.
B. Cost saving and efficiency improvement
Through effective treatment of waste copper wire, enterprises can save production costs and improve production efficiency, while reducing the impact on the environment.
C. Importance of sustainable development
The application of this type of equipment promotes the sustainable development of industrial production, transforms waste resources into useful resources, and makes an important contribution to the cause of environmental protection.
SUNY GROUP developed the industrial small copper wire granulator is important to promote resource recycling, improve production efficiency and achieve the goal of sustainable development. It not only plays an important role in the industrial field, but also makes a positive contribution to the cause of environmental protection. If you have the need, please feel free to contact us for consultation.
Circuit Board Recycling Equipment in Romania
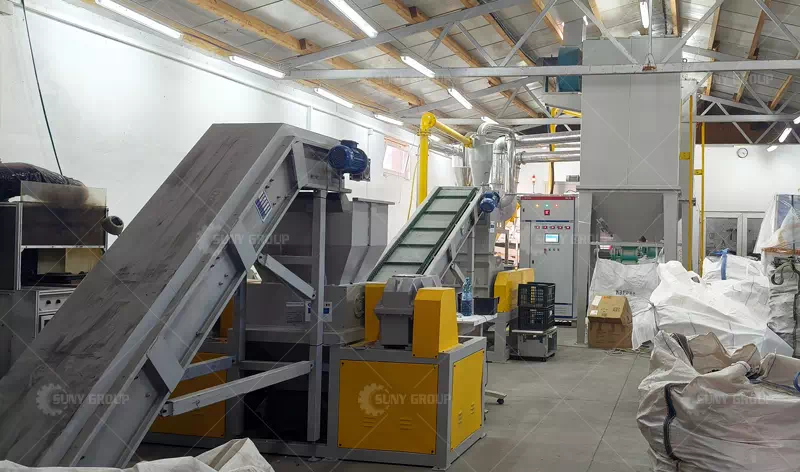
Circuit Board Recycling Equipment in Romania
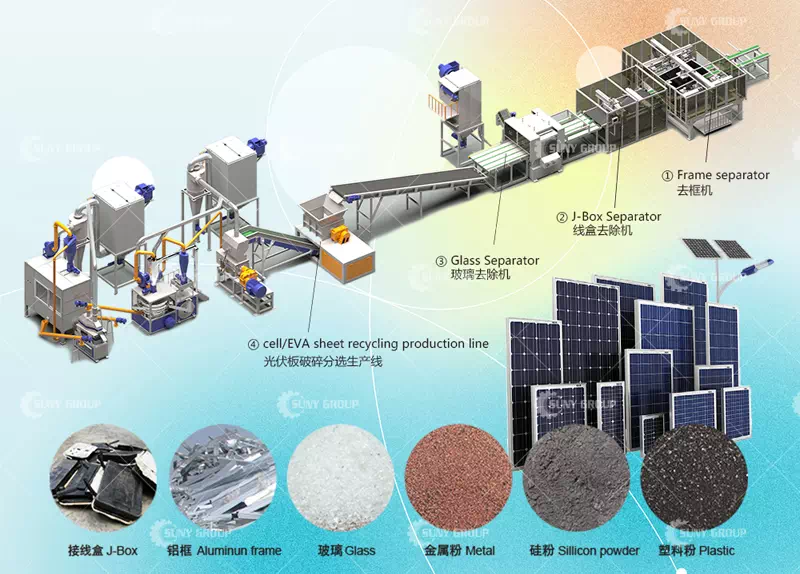
Solar photovoltaic panels are typically made up of a variety of materials, including silicon, glass, plastics and metals. The recycling of these materials requires efficient and specialized equipment to ensure that as much of the resource as possible is reused. Currently, around 90% of the materials used in PV panels can be recycled globally, but the actual recycling rate is well below this potential.
Solar PV Panel Aluminum Frame Remove Machine
Advanced recycling equipment
The selection and configuration of equipment is critical in the PV panel recycling process. Below are some of the key pieces of equipment and their functions:
Disassemblers: Disassemblers are used to separate the various parts of a PV panel, in particular the glass, the aluminum bezel and the silicon modules. The efficiency of this process has a direct impact on subsequent recycling.
Crushing equipment: Crushing equipment refines the dismantled material to ensure that the various types of material can be separated. The design of this equipment often includes multiple stages of crushing to accommodate different material hardnesses and structures.
Sorting Machines: The use of advanced sorting technologies (e.g., airflow sorting, magnetic sorting) allows for the rapid sorting of different materials. Sorting machines are able to effectively differentiate between different components such as glass, metal and plastics to improve recycling efficiency.
Extraction equipment: For precious metals (such as silver and gold) in PV panels, extraction equipment can separate them by chemical or physical methods. The recovery value of these metals is high, so their extraction process needs to be sufficiently delicate and safe.
Environmental benefits of the equipment
Recycling of PV panels not only helps to reuse resources, but also reduces environmental pollution. According to the Environmental Protection Agency (EPA), proper recycling reduces greenhouse gas emissions and decreases the need for new materials, thereby conserving natural resources. Modern recycling equipment often operates with energy-efficient and low-emission designs, further enhancing its environmental benefits.
Market Outlook for Recycling Equipment
With the global focus on renewable energy and sustainability, the market for recycling PV panels is growing rapidly. According to market research organizations, the demand for PV panel recycling equipment will increase significantly in the coming years. Companies investing in state-of-the-art recycling equipment will not only increase their recycling rates, but will also be able to gain a competitive edge over their competitors.
Recycling of photovoltaic panels is an important part of achieving sustainable development, and specialized recycling equipment is key to driving this process. Through efficient dismantling, fragmentation, sorting and extraction equipment, we are able to effectively recycle and reuse the valuable resources in solar and PV panels.
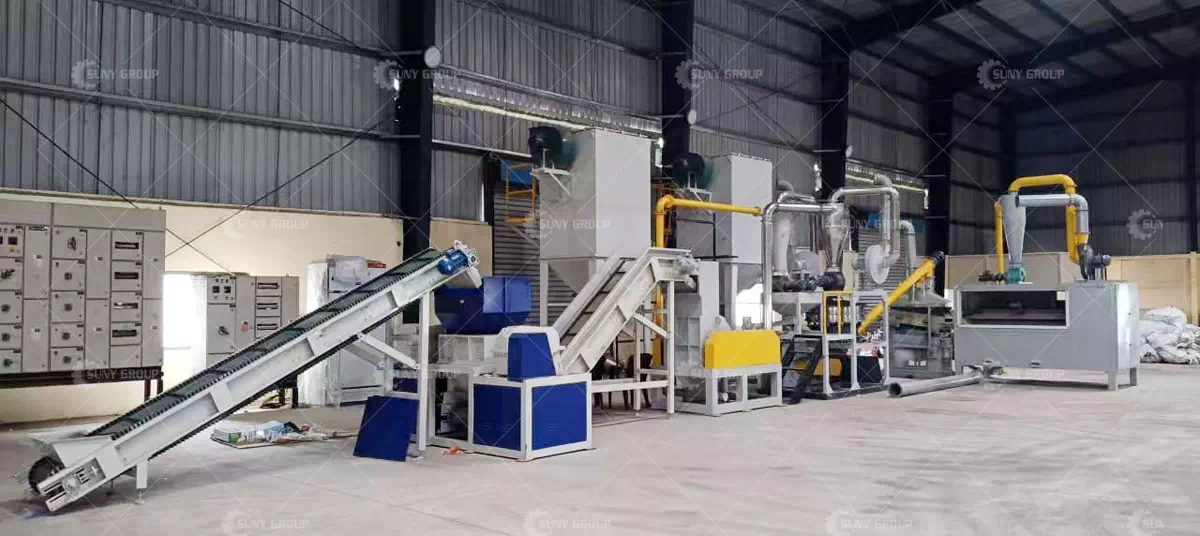
Indian Customer’s E-waste Recycling Production Line Site
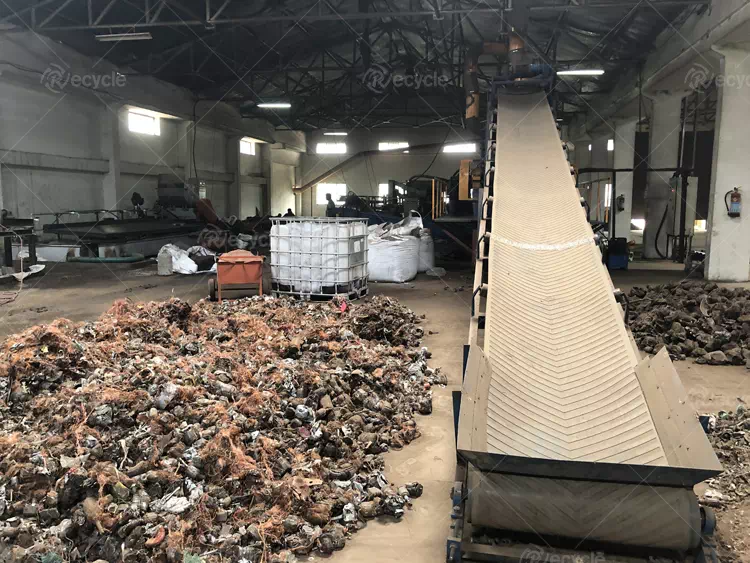
Scrap motor crushing sorting and recycling machines play a vital role in the disposal of scrap motors and resource recovery. These machines combine crushing, sorting, and recycling features to help companies efficiently dispose of scrap motors and recover valuable materials. Let’s delve into the key features and roles of these machines:
Crushing function: scrap motor crushing sorting and recycling machines can effectively crush scrap motors and break down the materials inside the motor into smaller particles, laying the foundation for subsequent processing and recycling.
Shreadder Machines and Motor Dismanteling Machines
Sorting function: these machines can sort the crushed materials and separate valuable metals such as copper wires and other materials from the waste materials, creating conditions for resource recycling.
Recycling function: By crushing, sorting, and recycling waste motors, these machines can effectively recover metals, plastics, and other valuable materials, promoting resource reuse and recycling.
Environmental significance: the use of waste motor crushing, sorting, and recycling machines helps to reduce the pollution of waste motors to the environment and promote the sustainable use of resources, in line with the concept of environmental protection and sustainable development.
Application areas:
Waste motor processing plant: these machines play a key role in waste motor processing plants, helping companies to efficiently process large quantities of waste motors and realize resource recovery.
Metal Recycling Plants: Scrap motors contain a lot of valuable metals, these machines can help metal recycling plants to effectively recycle the metal resources in scrap motors.
The scrap motor crushing, sorting, and recycling machine has an important role in the field of scrap motor processing and resource recycling, which provides effective technical support for enterprises to realize resource reuse, environmental protection, and sustainable development. Its crushing, sorting, and recycling functions transform the scrap motor into valuable resources, promoting the development of a circular economy and resource utilization efficiency.
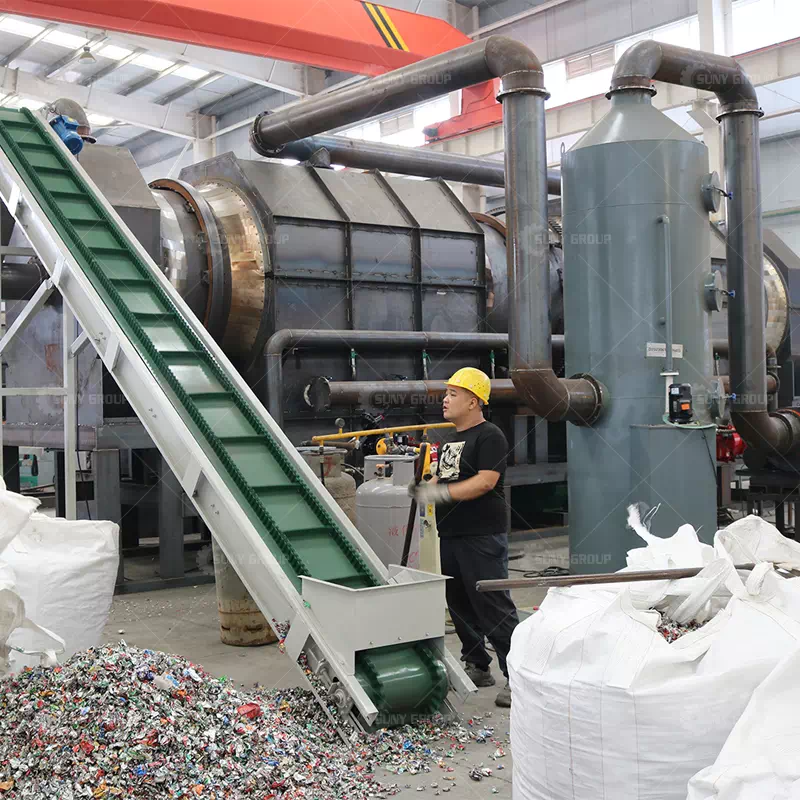
In the waste recycling industry, Continuous Charcoal Oven Paint Removal Equipment is a key machine that is specifically designed to separate paint from aluminum cans. This equipment plays a vital role in the processing of used aluminum cans, helping recycling plants to efficiently remove paint from the surface of aluminum cans, thus making the aluminum material easier to recycle.
1. Equipment Principle
The Continuous Charcoal Oven Paint Removal Equipment completely removes paint from the surface of aluminum cans by means of high-temperature charring. This equipment operates in a continuous mode and through a unique heating and treatment process, the paint on the surface of aluminum cans is carbonized into a form that can be easily separated.
Machine That Separates Paint from Aluminum Cans
2. Workflow
The equipment will feed the used aluminum cans into the charring furnace and undergo a high-temperature charring process, which causes the paint to decompose into gas and ash at high temperatures and separate from the aluminum cans. Subsequently, the separated aluminum cans can be further processed for recycling.
3. Advantages and features
High efficiency: Continuous operation improves the processing efficiency, allowing a large number of aluminum cans to be quickly removed from the paint.
Environmentally friendly: the gas and ash produced during the carbonization process can be effectively disposed of, reducing the negative impact on the environment.
Energy-saving: The use of advanced heating technology reduces energy consumption and improves the energy-saving performance of the equipment.
4. Field of application
This continuous carbonization furnace paint removal equipment is widely used in the recycling industry of used aluminum cans, which helps recycling factories process a large number of used aluminum cans efficiently and provides reliable raw materials for the production of recycled aluminum materials.
Continuous Carbonization Oven Paint Removal Equipment plays an important role in the recycling industry of used aluminum cans and provides reliable support for the production of recycled aluminum materials by efficiently removing the paint on the surface of aluminum cans. The application of this equipment not only improves the recycling efficiency but also helps to reduce environmental pollution and promote the sustainable use of resources.
Lithium-ion Cell Recycling Production Line
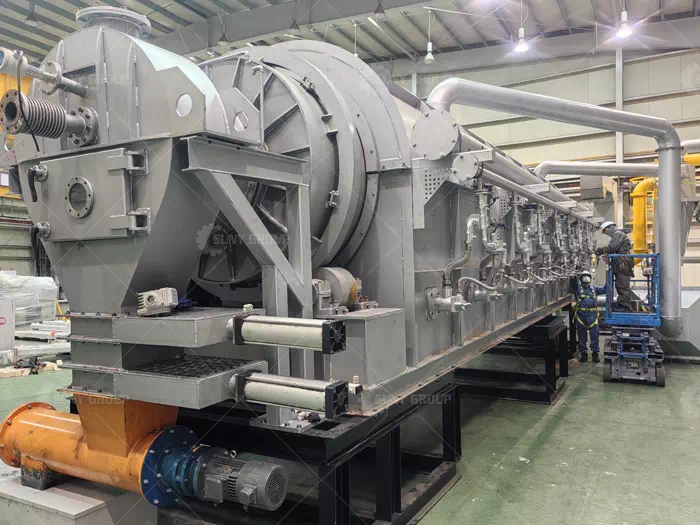
In today’s society, the demand for lithium-ion batteries is increasing with the popularization of electric vehicles, portable devices, etc., and the ensuing problem is the disposal and recycling of used lithium-ion batteries. The Lithium-ion Cell Recycling Production Line was created to solve this problem effectively.
Lithium-ion Cell Recycling Production Line is a production line specialized in the treatment and recycling of used lithium-ion batteries. It uses advanced technology and equipment to efficiently break down used batteries, extract valuable materials, and reuse them. This not only helps to reduce dependence on natural resources but also effectively reduces the environmental pollution caused by used batteries.
Lithium-ion Cell Recycling Production Line
In the Lithium-ion Cell Recycling Production Line, used batteries are first sent to the decomposition area, where they undergo a series of physical and chemical treatments to separate the battery shell from the internal materials. Subsequently, valuable metal elements, such as lithium, nickel, and cobalt, can be extracted through melting and dissolving methods and used to produce new batteries or other products.
In addition to the recycling of metal elements, the Lithium-ion Cell Recycling Production Line also focuses on the environmental protection treatment of batteries. Through reasonable waste water treatment, exhaust gas treatment and other measures to minimize the impact on the environment, to ensure that the production process meets environmental standards.
Overall, the Lithium-ion Cell Recycling Production Line plays a crucial role in treating used lithium-ion batteries. It not only helps to recycle resources but also helps to protect the environment and promote green development. It is believed that with the continuous advancement of technology, Lithium-ion Cell Recycling Production Lines will play an even more important role in the future, creating a cleaner and more sustainable production and living environment for human beings.
Customer Shredder Site in UAE
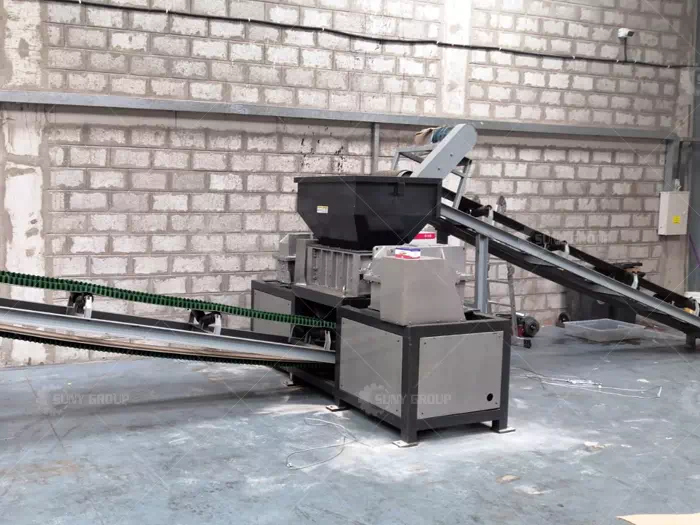
Customer Shredder Site in UAE
Fishing Net Shredder for Recycling
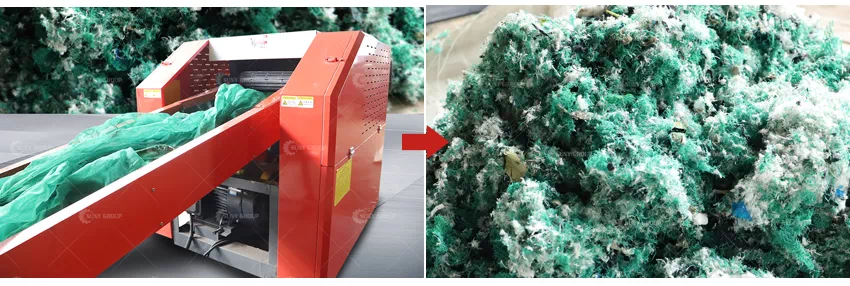
Fishing nets, which are mainly made of materials such as nylon, polyethylene, or polypropylene, are durable and prevent environmental degradation. Recycling discarded fishing nets not only helps to minimize the impact on the environment but also provides an opportunity to recycle valuable raw materials.
A fishing net shredder is a specialized machine designed to shred large, bulky fishing nets into small, manageable pieces. The initial shredding process is vital for efficient recycling, as it prepares the material for further processing (e.g. melting, pelletizing, or reuse in new products).
How it works
Loading the nets: The recycling process begins by feeding the waste nets into the shredder’s hopper. Depending on the size of the nets, some shredders may need to pre-cut the nets into smaller pieces to fit the machine.
Cutting and Shredding: Once the net enters the shredder, rotating blades or knives begin to cut the material into smaller pieces. These blades are designed to handle tough, fibrous materials such as nylon, ensuring that even heavily tangled nets are effectively shredded.
Output: After shredding, fishing nets are cut into smaller pieces or strips that are easier to transport and process. These pieces can then be melted down and converted into pellets for use in the manufacture of a variety of products.
The shredding process ensures that large fishing nets that would otherwise be difficult to transport or recycle become manageable for the next stage of recycling.
Advanced technology for fishing net shredders
Modern fishing net shredders have come a long way with the incorporation of innovative technology. Some of these latest features include
High durability: Cutting blades are often made of high-grade steel to withstand the tough, fibrous nature of fishing nets.
Automation: Many shredders are equipped with automatic feeding systems and sensors that adjust the shredding speed to the load, ensuring smooth and efficient operation.
Energy Efficiency: Newer models of shredders prioritize energy efficiency and reduce the environmental impact of the recycling process itself.
Dust and Fiber Control: Some shredders are designed with filters or systems that minimize the release of fine particles or fibers during the shredding process, helping to maintain a clean and safe working environment.
The fishing net shredder developed by SUNY GROUP will play a vital role in eliminating marine pollution and supporting the circular economy. Through continued investment and collaboration, the recycling of discarded fishing nets can significantly reduce their environmental impact and create new opportunities for resource recovery.